The synthesis of technology with industrial operations has ushered in a new era of productivity and efficiency, with the automatic feeding line being a prime example of this evolution. These advanced systems are essential in modern manufacturing environments, contributing significantly to optimizing resources while ensuring consistent and high-quality output. This article explores the multifaceted benefits of automatic feeding lines, drawing upon real-world applications and industry insights, underlining their indispensability in today’s manufacturing landscape.
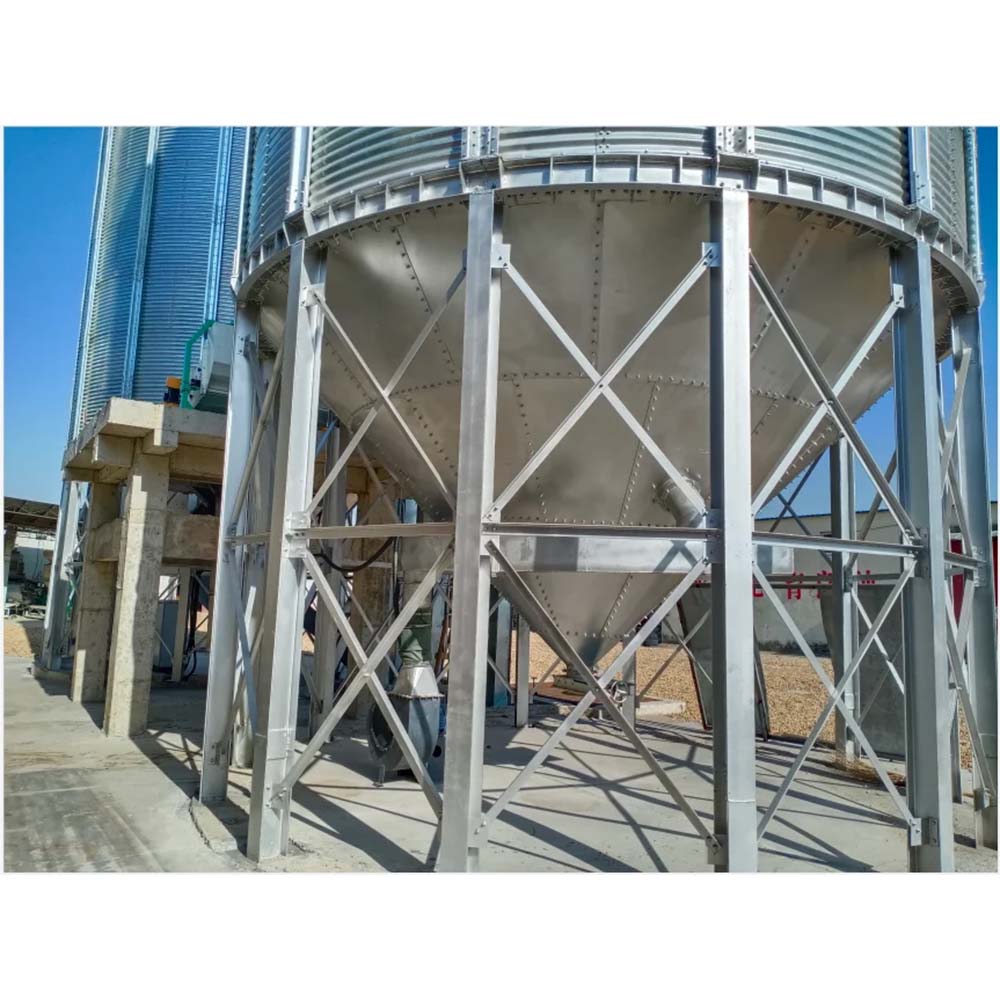
Automatic feeding lines have revolutionized the manufacturing process by automating the delivery of materials to various machine parts without human intervention. Companies investing in these systems benefit from an enhanced production capacity, as these lines allow for uninterrupted operation, reducing downtime associated with manual feeding processes. This automation not only maximizes efficiency but also leads to significant cost savings by minimizing labor costs and reducing the margin for human error.
Expertise in the field of industrial automation underscores the meticulous engineering that goes into designing and implementing an automatic feeding line. These systems are engineered for precision and reliability, pivotal traits that ensure they meet the rigorous demands of continuous production. Advanced sensor technology and cutting-edge software platforms are integrated to oversee and adjust the feeding process in real-time, accommodating various materials and production scales. This adaptability ensures that the automatic feeding line can evolve in parallel with the ever-changing demands of the market.
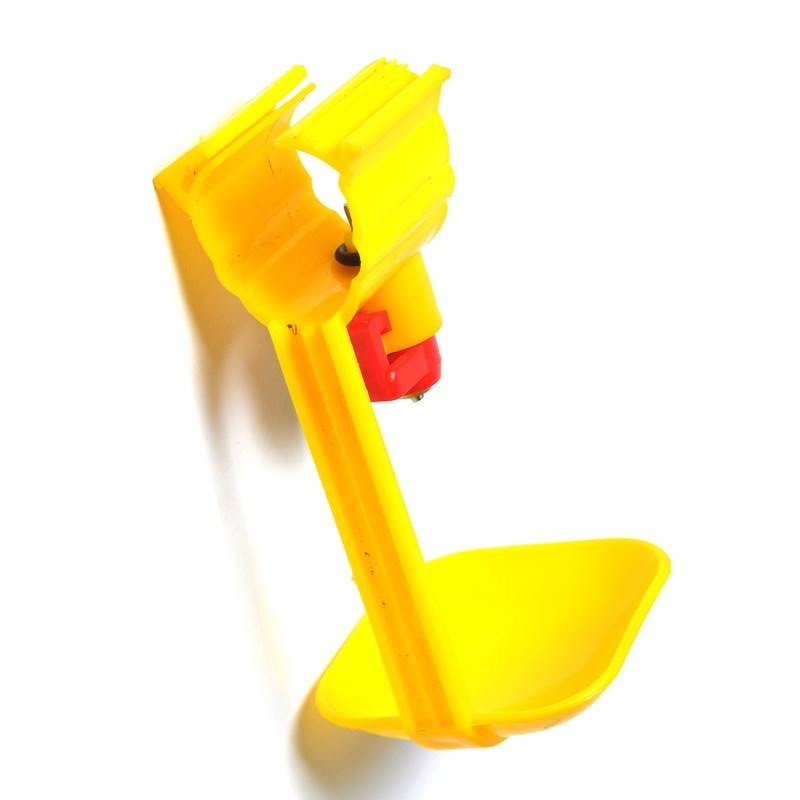
From an authoritative perspective, industry leaders have highlighted the role of automatic feeding lines in improving product quality. The consistent feeding mechanism ensures that materials are supplied at the optimal rate and in precise quantities, leading to a uniform product output that meets quality standards. Automated systems also diminish material wastage, as they are precisely calibrated to use only the necessary amount of materials needed for production, thus improving overall resource efficiency.
automatic feeding line
Trustworthiness is intrinsically linked to performance consistency and reliability, both of which are hallmarks of well-engineered automatic feeding lines. These systems are designed to operate under various production conditions and environments,
ensuring dependable performance. Moreover, regular maintenance protocols and system updates further contribute to their longevity and trustworthiness, assuring manufacturers of their investment's return over an extended period.
Real-world implementations of automatic feeding lines have showcased their transformative impact across multiple industries. In the automobile manufacturing sector, for instance, automatic feeding lines play a pivotal role in streamlining assembly processes, thereby reducing build times and enhancing throughput. Similarly, in the food and beverage industry, these systems are crucial in ensuring hygiene and consistency, as they minimize human contact with materials, adhering to stringent health and safety standards.
The integration of automatic feeding lines represents not just a leap toward operational efficiency but also offers a competitive edge in a saturated market. Companies adopting these systems can uphold faster delivery times and superior product standards, both of which are vital in establishing brand reputation and customer trust.
In conclusion, the multifaceted benefits of automatic feeding lines underscore their pivotal role in modern manufacturing. By enhancing production efficiency, ensuring quality consistency, and reducing resource wastage, these systems provide a strategic advantage that cannot be overlooked. As industries continue to evolve, the reliance on technology-driven solutions like automatic feeding lines will undoubtedly become more pronounced, cementing their status as an integral component of smart manufacturing. As such, stakeholders in the manufacturing space must seriously consider investing in these advanced systems to harness their full potential and drive future growth.