In the ever-evolving construction industry, the efficiency of materials management can make or break a project's success. A silo for a batching plant plays a pivotal role in this ecosystem by ensuring a seamless supply of essential materials like cement, fly ash, and other aggregates necessary for concrete production. This article delves into the cutting-edge design, operational advantages, and expert considerations crucial for selecting the right silo system for batching plants, all while ensuring optimal SEO benefits.
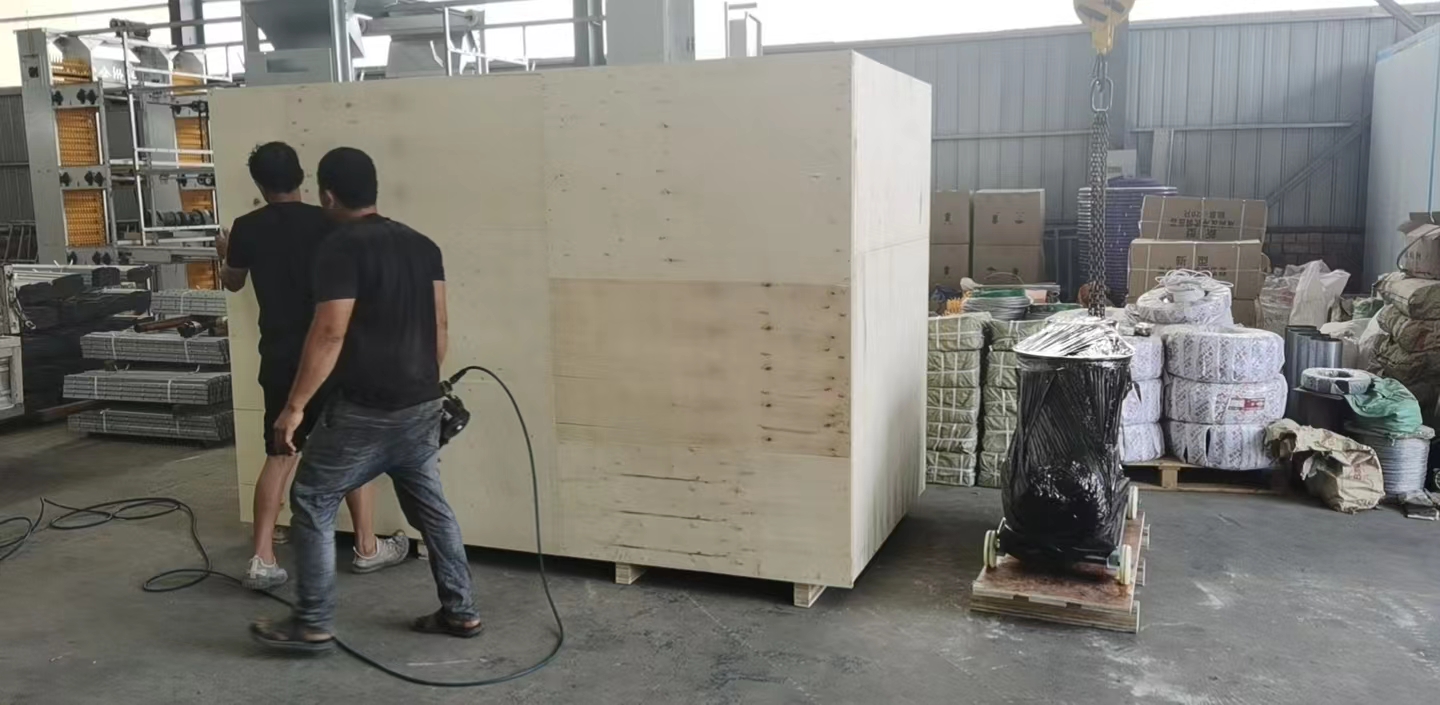
Silos are indispensable for the storage and management of bulk materials in batching plants, offering a structurally sound method to keep materials dry and readily available for production. These towering cylinders are engineered to maximize space while accommodating substantial quantities of materials, reducing the frequency of refills and minimizing downtime. The use of advanced materials such as high-strength steel and innovative engineering designs ensures that modern silos maintain structural integrity under various environmental conditions, bolstering their reliability and longevity.
From an expert's perspective, the operational efficiency of a silo is not merely defined by its storage capability but also by its discharge mechanism. A well-designed silo system is equipped with sophisticated unloading technologies that allow for precise dispensing of materials. Pneumatic systems, for instance, use air pressure to facilitate the smooth and controlled flow of materials, reducing waste and enhancing mixing precision in the batching plant. These systems are complemented by cutting-edge electronic controls for automated monitoring and regulation, offering seamless integration with the plant's overall operational systems.
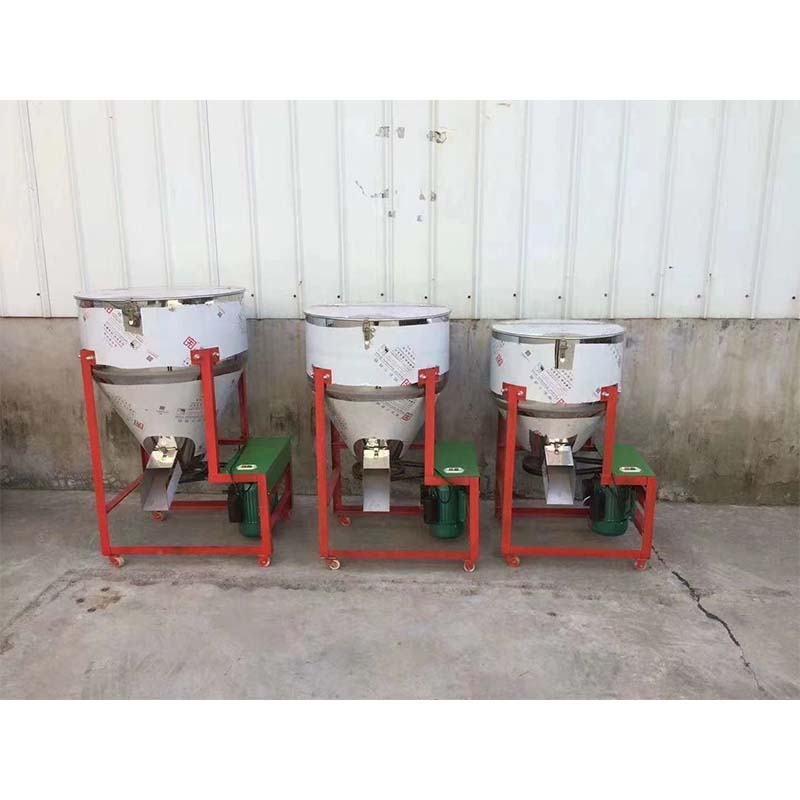
The authoritativeness of a silo system is further reinforced by its adaptability to industry-specific requirements. Customization options allow silos to cater to unique project demands, whether it involves specific material compositions or unusual site conditions. For instance, a batching plant operating in extreme weather conditions benefits immensely from insulated silo designs that maintain material consistency despite external temperature fluctuations. Such adaptable designs are often developed by leading experts in the field who have deeply studied the interplay between environmental factors and material integrity.
silo for batching plant
Trustworthiness in the context of silos for batching plants is underpinned by compliance with industry standards and regulations. Reputable manufacturers ensure that their silo systems adhere to stringent safety norms and quality benchmarks. This commitment to excellence is reflected in the use of corrosion-resistant coatings, high-quality seals, and failsafe operational mechanisms that guarantee safe and efficient operations over extended periods. When selecting a silo, it is crucial for project managers to prioritize systems that offer independent certification for occupational safety and environmental impact, thereby reinforcing the trust placed in these critical infrastructure components.
Innovation is at the core of modern silo systems, with a focus on sustainable practices to meet global environmental goals. Recent developments include the incorporation of solar panels to power the electronic components of the silo, reducing the overall carbon footprint of the batching plant. Moreover, ongoing advancements in material science have led to the development of eco-friendly construction materials for silos, enhancing their sustainability quotient without compromising on performance.
In conclusion, the efficacy of silos in batching plants hinges on meticulous design, operational precision, and unwavering adherence to safety and quality standards. For stakeholders in the construction industry, understanding these nuances is crucial for optimizing material management, enhancing plant efficiency, and ultimately achieving project success. As you navigate the complexities of silo systems, prioritizing established industry expertise and authoritative innovations will ensure your batching plant stands at the forefront of technological advancement, offering a competitive edge in a demanding market.