Unlocking the Full Potential of Scalding Tanks A Comprehensive Guide to Enhancing Your Processing Line
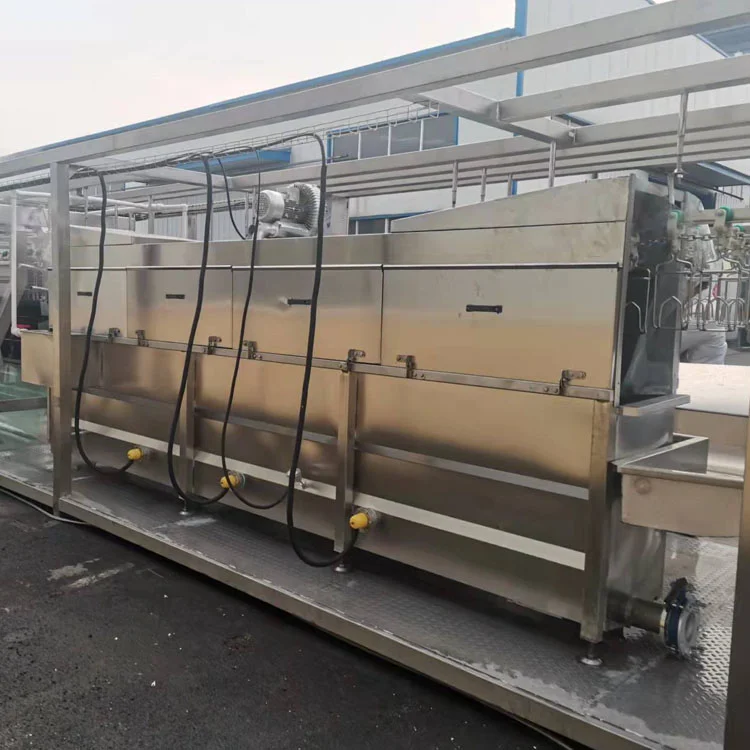
In modern processing systems, particularly in the food and agricultural sectors, scalding tanks are pivotal. These units play a crucial role in preparing products through controlled heat application. Understanding the nuances of their operation can significantly enhance efficiency, product quality, and compliance with safety standards.
Scalding tanks are primarily used to loosen feathers on poultry or the hairs on swine before further processing. This preparatory step is essential to ensure that subsequent processing stages are effective and that final product quality is not compromised. To better appreciate the impact and optimization of these tanks, we explore some real-world experiences, expert insights, and industry standards that underline their critical importance.
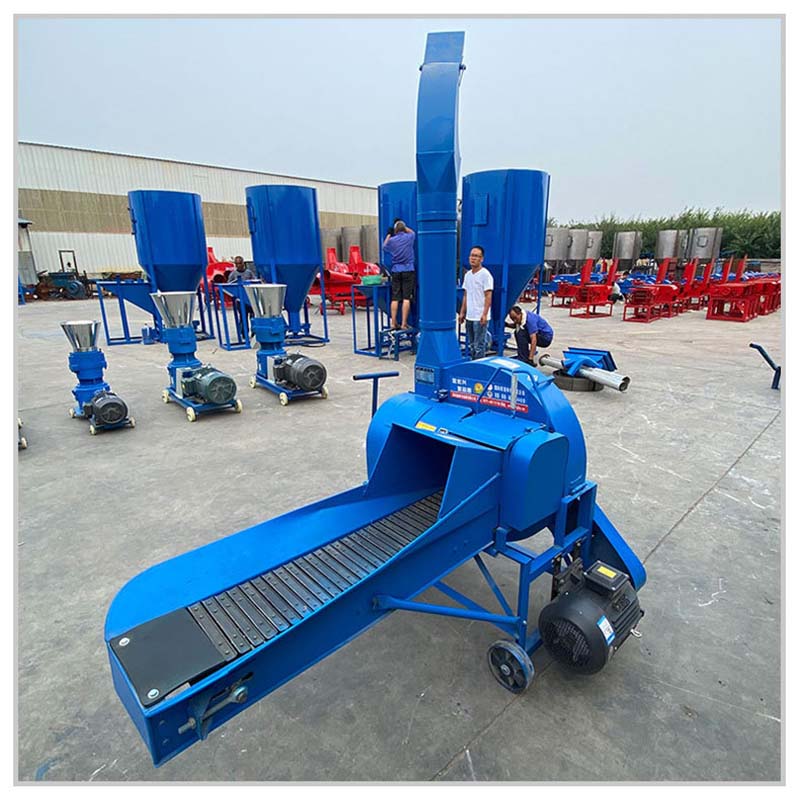
Experience in the field has shown that the correct usage of scalding tanks can dramatically affect processing efficiency. For example, a poultry processing facility in the Midwest was able to reduce defeathering time by 20% by simply calibrating their scalding tank temperature settings to align more closely with optimal ranges for chicken. This adjustment not only increased throughput but also reduced energy consumption, leading to cost savings. These firsthand accounts underscore the importance of both equipment maintenance and operational precision.
From an expertise standpoint, understanding the technical specifications of scalding tanks can greatly enhance their utility. Key features such as temperature control systems, agitation mechanisms, and tank size should be tailored to the specific needs of the processing line. Expert recommendations suggest maintaining water temperatures between 125°F and 130°F for poultry to ensure optimal loosening of feathers without compromising skin integrity. Similarly, for swine, maintaining the temperature at around 136°F is crucial. These temperature guidelines are essential, but they must be adjusted based on specific facility requirements and equipment capabilities.
scalding tank
Moreover, the authoritativeness of best practices surrounding scalding tanks provides a framework for their optimal use. Established industry guidelines often highlight the benefits of integrating automated systems that monitor and adjust tank conditions in real-time.
Such systems can lead to minimized human error, ensuring consistent product quality. Case studies from leading processing companies reveal that facilities leveraging automation in their scalding tanks report improved consistency in product output and a reduction in labor costs.
Trustworthiness in scalding tank operations is not only about maintaining equipment functionality but also about adhering to food safety standards. Tanks that are inadequately cleaned or improperly regulated can become breeding grounds for bacteria, posing serious food safety risks. Thus, regular sanitation protocols and compliance with health and safety guidelines are imperative. Many companies conduct bi-weekly audits of their scalding operations to ensure adherence to safety standards, safeguarding both consumer health and brand integrity.
The incorporation of innovative technologies can further enhance the trustworthiness and effectiveness of scalding tanks. For instance, implementing digital sensors and IoT (Internet of Things) technologies can provide critical oversight. These tools offer real-time data on water temperature, pH levels, and operational status, enabling proactive maintenance and immediate adjustments when necessary. This technological layer adds a level of traceability that is increasingly demanded by both regulators and consumers.
As the role of scalding tanks continues to evolve, staying abreast of technological advancements and industry standards ensures competitive advantage. Integrating advanced materials such as corrosion-resistant stainless steel can prolong the lifespan of scalding tanks, reducing maintenance downtime and ensuring consistent operation. Furthermore, staff training programs focusing on equipment operation and safety practices can empower employees, ensuring that they utilize these tools to their full potential.
In conclusion, scalding tanks are an integral component of efficient and effective product processing. Through experience-driven insights, technical expertise, authoritative industry practices, and trustworthy regulatory compliance, businesses can optimize their scalding operations. Maximizing the potential of these tanks not only boosts operational efficiency but also enhances product quality and safety, ultimately contributing to the success and reputation of processing facilities.